The Digital Archaic Heraion Project is one of the first studies of ancient architecture wholly based on 3D documentation. The creation of this 3D ‘virtual museum’ progressed in two phases: scanning in Corfu, and post-processing the models for publication. The complete corpus of 550 inventoried architectural fragments in the Corfu museums was scanned in 3D during the Fall of 2010. The resulting models were processed and released online in 2011.
The original, high-resolution scan data is made available as material is published in print—currently 69 models can be downloaded from the individual object pages, and the remainder will be released by the final publication of the architecture (currently in preparation). Likewise, the methodologies used for creating the 3D models and archive will be presented on this website in detail after their publication in print.
The scanning of the Mon Repos corpus went surprisingly quickly. The project made use of a Creaform VIUscan handheld scanner (2010 model), a portable device that not only captures the shape of an object, but also records surface colors. The scanner creates a model relatively quickly: a small fragment (below ca. 10 cm across) might take minutes, whereas the largest fragment at Mon Repos, the lion-waterspout MR1, took 4 hours to record. In all, the scanning of the 550 fragments in the Corfu museums was completed in 35 days.
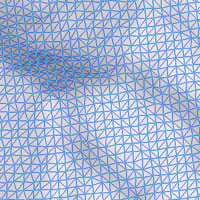
Triangle mesh and texture
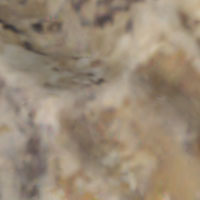
Of course the time to finish a scan varies considerably depending on the size and complexity of the object, and the quality settings for the scanner. The VIUscan is capable of producing a facetted polygonal mesh with edges as small as 0.1 mm. In practice, however, this is so much detail that the laptop recording the measurements is quickly overwhelmed. Most objects at Corfu have been scanned at resolutions closer to 1 mm, ranging from 0.5–2.0 mm. The scanning progressed much more rapidly, and the resulting models have more than enough detail to record the critical features of objects 10-80 cm across. The 3D models are not a perfect replica of the original object, since they have been reduced to a grid of measurements no finer than 0.5 mm. Small features and edges have been blurred.
The VIUscan is equipped with a camera that simultaneously records the colors of the surface being scanned. The photographic color information is stored as a separate 2D image, or ‘texture map’, whose coordinates are stored in the 3D geometry. The resolution of the texture map varies, but under the best possible conditions the VIUscan camera can record up to 10 samples per mm—an individual pixel as small as 0.1 mm. In practice, the camera has difficulty creating a sharp image with more than about 8 samples per mm. The objects at Mon Repos have been scanned with texture resolutions ranging from 4–8 samples per mm, which means that the photographic detail is about 5 times higher than the geometry of the model.
The VIUscan is a ‘structured light’ scanner, which projects a laser-light pattern over the object in order to reconstruct contours in 3D. In order to record all the surfaces of an object, the operator moves the scanner slowly around it by hand, as seen in the following video.
Scanning a portrait bust in Corfu (video speed x2)
Because the VIUscan is constantly moving during the scanning process, it must keep track of its position by reference to fixed points. This model of scanner uses a network of ‘positioning targets’, small white reflective dots from which the scanner can estimate its location and orientation. In the video, the black board under the portrait bust held most of the positioning targets, and a small number were placed on the bust as well. Because the targets placed on the object hide its surface, the scanner must guess the original surface geometry and texture under the targets. The dots are relatively small, and they have been placed on damaged or uniform parts of the object in order to preserve the more important details of the object.
The network of targets must be absolutely stable during the scanning. As a result, only the top half of the bust could be scanned at one time without disrupting the dots—the back of the head was scanned later, using an unrelated grid of positioning targets. Some Corfu objects could be scanned in one pass, but the majority were recorded in two separate coordinate systems: one for the top and one for the bottom.
The color-textured 3D models created by the scanner are incomplete meshes which require further manipulation. First, the separate pieces for the top, bottom, or additional segments must be united into a single object mesh. Second, the scans have minor errors, such as gaps in the texture set to a dark blue color, and small holes in the triangles composing the 3D mesh. Third, the mesh generated by the scanner is generally higher resolution than necessary. It should be simplified to improve the speed of display and for compression, which is critical for distribution over the Internet.
Many of these operations can be performed by an open-source 3D processing package, MeshLab. However, Geomagic Studio, a commercial package, was used for processing most of the Corfu scans because of its superior stability and tools.
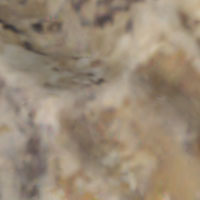
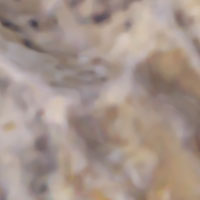
Texture maps before and after processing
Minor structural flaws in the mesh have been repaired using automated post-processing tools. Tiny gaps in the texture map are also filled using an automated algorithm in Adobe Photoshop. For several fragments mounted on display in the museums, it was impossible to acquire textures at the back, and instead a neutral color has been filled into these missing areas.
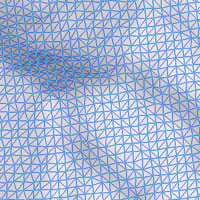
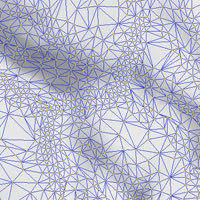
Mesh before and after decimation
The processed 3D models of the Mon Repos fragments typically have about 150,000 triangular faces (range of 25,000–800,000 faces), record features as small as 1 mm, and have a color texture resolution of about 5 pixels per mm (range of 2.5–6 pix / mm). The preview 3D models currently available from the embedded viewer have been greatly simplified, however, due to the limitations of 3D-graphics support in web browsers, and the prohibitively large size of the processed models (10–50 Mb). The websites's preview 3D models have been reduced to 4,000–16,000 faces, and the resolution of some textures has been reduced.
There are multiple sources of potential error in the 3D scans presented here. The VIUScan's manufacturer's specify an 1–σ error of 0.02 mm locally, which means there is a quantifiable but insignificant error in the positions of each 3D point measured on the Mon Repos objects. However, the effective error is much higher.
First, the scanner relies on targets to determine its location, but the positions of the targets include a measurement error up to about 2 mm over a meter. In other words, a 2-m-long object might have a 4 mm warp introduced by inaccurate survey of the positioning targets. Because the largest Mon Repos fragments do not greatly exceed a meter in length, it is unlikely that the absolute overall error ever exceeds 2 mm. Early in the Corfu project, a number of smaller objects were scanned with a piece of plexiglass between the scanner and the object, which created a potential error of 1–2 mm.
Another source of error is introduced during post-processing, when separate scan segments are stitched together into a unified model. Because the separate top and bottom scan segments have unrelated coordinate systems, it is necessary to extrapolate their original relationship by matching corresponding points on the two scans. While this process can be relatively precise, an additional absolute error of ca 1 mm is still possible. Finally, the various repairs and decimation of the mesh make minute changes in the geometry of the 3D mesh, although these alterations are unlikely to exceed 0.5 mm.
Despite all of these potential sources of error, most of the 3D models from Mon Repos are accurate to less than 1 mm. The greatest potential cumulative error for the largest objects is 1–3 mm.
The color textures are a detailed record of the original object's surface, but gaps have been patched seamlessly in the post-processing. Like a photograph, the textures on the 3D models can appear realistic, but the colors vary with lighting conditions and cannot be used for exact colorimetric measurements.
Metadata describing the quality of each scan will be made available for each object with its high-resolution scan. The metadata will include notes on the resolution of the 3D model's geometry and texture, the scanning conditions, and the estimated maximum error for each of the objects.

The Archaic Sanctuary at Mon Repos, Corfu, is licensed under a Creative Commons Attribution-NonCommercial-NoDerivs 3.0 Unported License, and maintained by the Center for Digital Research in the Humanities. Please direct any questions to the site administrator.